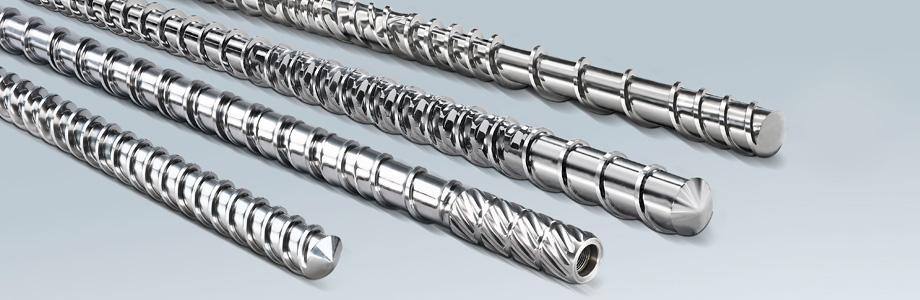
Extrusion Screws Designed for Optimal Performance and Extended Life
At TizaTech, we show our customers how to optimize processes, avoid costly repairs and extend the life of valuable components. We know general purpose parts rarely meet the demands of ever changing technology. Our decades of experience with extrusion screw design allows us to work with every aspect of plastics. Everything from compounding to blown film, we specialize in producing screws for premium color mixes with the most efficient compounding and throughput. At TizaTech, we’re known for offering the highest quality parts with a variety of extrusion screw solutions including:
Carefully engineered screw geometry to match the exact needs of your process;
High throughput, supreme mix and melt quality for optimum component life;
Screw and Barrel solutions for new processes and products;
Screw recovery solutions for high performance and multiple applications;
Quality inspections with every step of the process to create customized parts specific to our customers demands;
On-site Consulting and Field Services.
Our extrusion screws enable you to maximize extrusion throughput, product quality and component service life. We can offer you all kinds of screws for extrusion: 3-zone screws, multiple thread screws, barrier screws, vented screws, or highly complex twin screws.
Single Screw Extrusion
Extrusion is a technology to convey materials which dates back far before the plastic era. It has been in use in the ceramics industry for ages. When we also include screws to transport water,the technology is thousands of years old.
For plastic processing, extrusion has been used from the start. First to convey PVC and polyethylene, later also for engineering plastics. However, screw modifications become necessary.
The length of a screw is expressed as theratio between diameter and length. For a 21 D screw with a diameter 3 cm, theactive length is thus 63 cm. Since the emergence of crystalline engineering plastics, the length of the screws had to be increased. A screw length of 24 D is quite common. The geometry of screws can be varied.Widely used for extrusion applications are 3-zone screws and barrier screws.
3-zone screws consist of 3 zones: Feed Zone, Compression Zone, Metering Zone
The feed section is the part of the screw where the unmolten polymer enters into the barrel. The rotating screw moves the material along the heated barrel where it starts to melt.
In the compression zone, gases like air and volatiles like moisture, are being removed. In the compression zone, the flight depth decreases and gases are pushed back into the direction of the hopper.
Finally, the material enters the metering section. In this section, pressure is generated which enables the material to be conveyed into the shaping area, like feed block or film die.
The compression ratio of the screw is the ratio between the flight depth of the feed section and the ratio of themetering section.
Most screws have a flight helix that is equal to the diameter of the screw.
Feeding
To understand the mechanism of the conveying ability of the extruder screw, it is helpful to imagine a screw orbolt in a barrel. When the screw rotates any material between the screw surface and the barrel wall will be conveyed dependent upon the direction of rotation. Obviously, the extruder is designed to move the material from hopper to the front of the extruder.
Compression
Until the granules are molten, with every screw rotation, the material will be conveyed 1 speed. What has been conveyed is a mixture of roughly 50 % solids and 50 % air.
Without compression section, the molten material behaves like a foam. In the compression section, the volatiles are pushed back into the direction of the hopper.
The length of the compression section depends on the polymer to be extruded. The extreme example of PVC, the compression section comprised the full length of the screw. For crystalline polymers a very short compression section is recommended.
Metering
The molten and compressed polymer now enters the metering zone. The flight depth is less than in the feeding zone,but the flight depth is equal over its length.
The function of the metering section is to build-up pressure. The amount of pressure that can be build-up, depends on the length of the metering zone.
Mixing
All single screw extruders show some mixing effect, although very limited. For the proper dispersion of additives like stabilizers, antiblock agents, etc., mixing elements are being used.
There are various types of mixing sections,like Maddock, pineapple or pintype mixing elements.
Barrier screws
Another way of efficient mixing is using a barrier screw. Using this type of screw, the polymer is forced over the flights of the screw into a second channel.
Applications:
1. Film Extrusion: Blown Film and Cast Film Extrusion and Co-Extrusion
2. Plastics Recycling: HDPE/LDPE/LLDPE/PP film recycling and regranulating, pelletizing, used in vent/double vent degassing extruders and cascade extrusion lines; Non woven Spun-bond PP recycling and pelletizing; Nylon/PA net recycling and repelletizing
Keywords: Extruder Screws, Extrusion Screws, Extrusion Feedscrews, Replacement Extruder Screws,
Keywords in Various Languages: husillos bimetálicos, husillos nitruración, husillos de extrusión, husillos para la extrusión, extrusión monohusillo, husillos nitrurados como bimetalicos, husillos y cámaras para diferente tipo de maquinaria de plástico (inyección, soplado y extrusión); układy plastyfikujące, ślimaki azotowane, wzmocnione, chromowane, ślimaki i cylindry do wtryskarek i wytłaczarek;